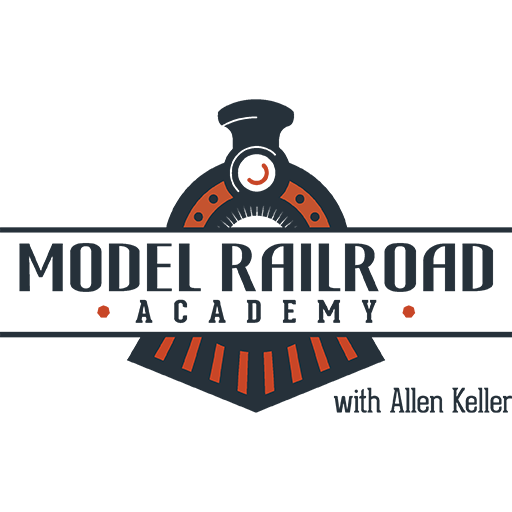
Laying Model Railroad Track: Tips and Tricks
MRA EditorsAny proficient modeler knows, if you take your time and apply the necessary effort to build good, sturdy model railroad track, your layout is going to last you a long, long time. Conversely, if you rush through the process of designing and installing model railroad track and you don’t pay attention to the details, you’ll find yourself pulling up and redoing the tracks sooner rather than later.
As with many other aspects of a model railroad layout, when it comes to trackage we’re strong advocates of starting with a plan and working step by step through the entire process until you’ve created something of which you can be proud. So in this lesson, we teach you the surefire tips and techniques necessary to lay model railroad track that’s durable, neat and fully customizable.
How to lay model railroad track that will last
Laying model railroad track begins with mapping out your design and ends with wiring and connecting to a power source. To help you get from start to finish, expert modeler Tom Lund walks you step by step through the process of laying trackage, from tracing turnouts to testing the rails. You’ll learn how to customize and build each of the essential components of solid model railroad track using simple tips and techniques.
To demonstrate the entire procedure, Tom builds out a sample segment of a model railroad track. He shows you the correct way to cut, adhere and sand cork roadbed, which will serve as the base of your model railroad track, then explains how to trim rail joints, install a turnout throw and solder a power source so you can control your turnouts. With these expert tips for designing and building a model railroad track, you’ll be able to create trackage that not only holds up over the years, but also makes your layouts look immaculate!
Track work can make or break a layout. Good track work can actually improve how trains run, and reward you with years of trouble-free operation. On the other hand, poor track work can be a never-ending source of frustration. Let's start by transferring our layout plan to the plywood. I sketch my track plan onto the plywood using a straight edge and pencil.
I keep parallel tracks about two and an eighth inches apart. Use two and a quarter if you use tight curves or full length rolling stock. This allows for clearance. Locate your turnouts first. I photocopied left and right hand turnouts so I could try different configurations.
Use spray adhesive to them to the plywood. I'm gonna put them right on the center line, and I'm gonna rub that down. Then connect the turnouts with a straight edge, using a permanent marking pen. And I'll use a few nails to line up the ends, and I can adjust this to what I want. So I like my curve about there.
So I'm gonna put a nail in there to hold it. A few nails and a ruler form smooth curves. Finally, mark your turnout throw position. Now that we have our turnouts in place, and connected them with our tracks center line, it's time to put down the roadbed. Cork is an inexpensive and effective roadbed.
The first step is to butt the cork to the center line, using yellow glue. Push pins work well to hold the cork in place until the glue dries. Follow the outside curve first, then follow with the second piece of cork on the inside. You can cut pieces to fit the gaps. So, I'm gonna take a straight edge and a razor blade.
Gonna come to the point here. Then I'll glue this one in. Once the glue holding the corks had a chance to dry, pull out the pins. We're gonna use a sanding block to smooth the cork. A flat, smooth surface ensures trouble-free track.
There's often a ridge when breaking apart the cork, so sand the bevel also. Locate the turnouts first, then connect with flex track. Code 83 flex track is popular with HO scalers. It's sturdy enough for good operation, yet isn't so big as to look toy-like. What I'm doing is locating turnouts, and you can kind of do on the center line of the cork.
And that'll give you a pretty good idea. Rail joiners not only connect the rail, but form them the electric connection also. Use a single edged razor blade to cut under the rail. This allows room for the rail joiners to slip in, and not leave a raised bump at the rail joint. Turnout throws are inexpensive, work well, and have a great railroady look to them.
The turnout throws have a pin that fits into the turnout. To put the turnout throw on the side opposite intended, match the cork to allow a plastic rod to carry a wire underneath the track. Foam board construction adhesive works great to hold the track in place. It sets up rapidly and adheres well to both the cork and the plastic ties. Use push pins to hold the track in place.
Now that the track's been laid, we can install the turnout throws. Build up to roadbed height, using strip wood. I'm gonna locate them, and then I'm gonna use a little yellow glue. I'm beveling the strip wood so it fits against the cork. It's important to center the turnout and the throw during installation for proper operation.
And that is gonna go right in the hole, like so. There is no need to glue the turnouts. Pre-drill the nail holes to prevent splitting of the wood. Use track spikes and set, so they touch the tie, but do not collapse it. And, voila.
Soldering rail joints makes for a seamless electrical path, as well as for smooth kinkless curves. For your power feed, drill a hole as close to the rail as possible. I use solid rather than stranded wire because it allows me to pre-fit to the rail before soldering. And if T]there's pressure on the rail before you solder, it'll make your soldering a lot easier. Now I'll use a rail car to check my joints.
I'll throw my turnout throw, I'll come through, try this one, and see how they work. Smooth track work is critical to the longterm enjoyment of your railroad. Take your time, and pay attention to the details. The reward will be years of trouble-free operation.
When I saw the instructor glue down the templates and lay the cork over the templates, I finally saw the way to ensure that the track would all be aligned nicely. I used AnyRail to create my small switching layout and Peco track/templates for my turnouts. This is my first real layout and the size of the module that he was building was ideal for me. This video was invaluable as I followed along step-by-step. Please pass along my appreciation to the instructor.
I did not hear you mention insulating the frog rails on the cross over. anyone duplicating this will have a short circuit. Otherwise, it was a very good primer for laying track
Great video with clear instructions.